This post is a paid partnership with Lowe’s! Thank you for supporting my sponsors! If you caught my post yesterday,…
Concrete

About Daniel Kanter
Hi, I'm Daniel, and I love houses! I'm a serial renovator, DIY-er, and dog-cuddler based in Kingston, New York. Follow along as I bring my 1865 Greek Revival back to life and tackle my 30s to varying degrees of success. Welcome!
Follow me everywhere
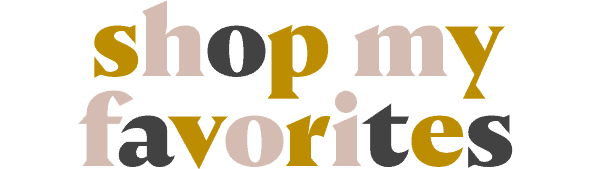
Archives: 2010-2022
Search
Popular Categories
This blog uses affiliate links. Sponsored posts are always identified clearly in the body of the post text and by using the “sponsored post” tag.