It’s Monday, so gather the family around the tube for About the Folks! Today we present the fourth and final episode in our 4-part docuseries on my friend John’s 1723 stone house. Having walked through bedrooms, bathrooms, the kitchen, the living room—even the attic!—we’re circling back to the first floor…
14 February 2022
About the Folks Episode 3!
It’s Monday morning, and you know what that means!!! Or, wait, do you? This is still pretty new for all of us. The third episode of About the Folks is here for your viewing pleasure! In this episode we explore one of my favorite parts of any old house—the attic—and…

About Daniel Kanter
Hi, I'm Daniel, and I love houses! I'm a serial renovator, DIY-er, and dog-cuddler based in Kingston, New York. Follow along as I bring my 1865 Greek Revival back to life and tackle my 30s to varying degrees of success. Welcome!
Follow me everywhere
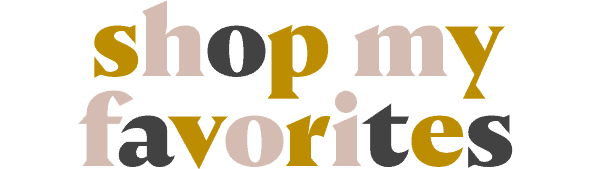
Archives: 2010-2022
Search
Popular Categories
Follow me on Instagram
Hello hello! It’s another release day! About the Folks Episode 2 has arrived! What is this? Let me tell you.…
It’s today, it’s today! After many months of scheming and plotting and shooting and editing, Juliet and I are so…
For years now, I’ve had this idea about doing something on my blog other than just talk about myself and whatever I’m doing.…
This post is in partnership with Article, who generously provided the featured furniture! Remember how we all just lived through…
Some of you know this story so I’ll try to keep the history lesson brief: way back in 2015, I…
This blog uses affiliate links. Sponsored posts are always identified clearly in the body of the post text and by using the “sponsored post” tag.