This post is in partnership with Lowe’s! Thank you for supporting my sponsors, who embraced my decision to delay the…
DIY Tutorials
This post is in partnership with my friends at Lowe’s! Thank you for supporting my sponsors! Did you see all…
This post is in partnership with Lowe’s! Thank you for supporting my sponsors! Remember how I said there were two…
This post is in partnership with Lowe’s! Thank you for supporting my sponsors! Do you recall, when last we spoke,…
This post is a paid partnership with Lowe’s! Thank you for supporting my sponsors! Let’s build some cabinets for my…

About Daniel Kanter
Hi, I'm Daniel, and I love houses! I'm a serial renovator, DIY-er, and dog-cuddler based in Kingston, New York. Follow along as I bring my 1865 Greek Revival back to life and tackle my 30s to varying degrees of success. Welcome!
Follow me everywhere
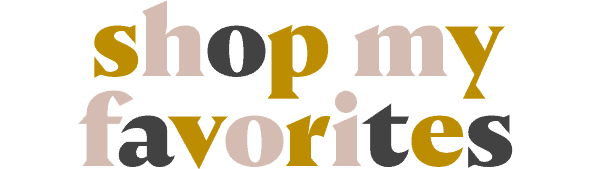
Archives: 2010-2022
Search
Popular Categories
This blog uses affiliate links. Sponsored posts are always identified clearly in the body of the post text and by using the “sponsored post” tag.