WELL. This has been a long time coming. About two and half years ago, I embarked on what’s likely the…
Exterior
This blog mini-series is in partnership with Lowe’s! Thank you for supporting my sponsors! Friends: I have picked up a new…
Here is a shocking bit of information that you have likely already deduced if you have read this blog for…
My bedroom has always felt…tricky. It’s a big enough room, but between three doors, three windows, and a radiator, it’s…
Now that it’s super nice outside, I’ve been trying to spend a little bit of time every week in the…

About Daniel Kanter
Hi, I'm Daniel, and I love houses! I'm a serial renovator, DIY-er, and dog-cuddler based in Kingston, New York. Follow along as I bring my 1865 Greek Revival back to life and tackle my 30s to varying degrees of success. Welcome!
Follow me everywhere
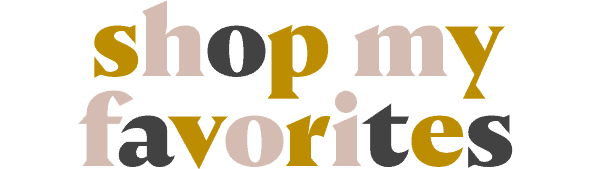
Archives: 2010-2022
Search
Popular Categories
This blog uses affiliate links. Sponsored posts are always identified clearly in the body of the post text and by using the “sponsored post” tag.